
Aquaculture - Bespoke Farmed Fish Processing System Reduces Rejection Rates, Increases Efficiency & Improves Productivity
An innovative and technical fish processing solution utilising KAESER OMEGA Exhausters has helped a market-leading Scottish Salmon producer to significantly improve its fish gutting and cleaning process for this important salmon farming process.
The bespoke vacuum system, co-designed and installed by specialist engineers from Kerr Compressor Engineers, has improved a previously flawed automated salmon processing system that was suffering from several issues causing high fish rejection rates (+10%) and requiring manual intervention.
The success of the new and improved system has since reduced rejection rates to under 1%, released manpower and increased efficiency while improving both quality and productivity.
Drawing on Experience & Working in Partnership
Harvesting farmed salmon is an intensive and important stage of a fish farm’s production cycle with thousands of quality-reared fish needing to be humanely despatched and processed in an efficient, timely and controlled manner.
Having invested heavily in specialist automated salmon processing equipment to transfer, slit, gut and clean their farmed stock across 4 separate processing lines, our customer was experiencing production issues and high rejection rates. The operational issues appeared to be related to the pneumatic system installed to operate the processing lines by the OEM / contractor as part of the larger project and installation.
Compressed air, nitrogen and fluid power specialists in Scotland for over 40 years and as an experienced, trusted supplier to the Scottish aquaculture industry, Kerr Compressors was asked to investigate, assess and make recommendations on how to resolve the processing plant issues while improving the reliability and energy efficiency of the specialist air system.
Working closely with our customer and in partnership with Derek Mayall of KAESER HPC (a very experienced blower and vacuum system specialist) and Adrian Feiler of KAESER Kompressoren (an Aquaculture air product specialist), Cameron Kerr (our experienced Aquaculture application specialist) requested the original drawings and schematics detailing the pneumatic system layout and components.
Having visited the impressive site and installation to inspect first-hand the complete system and to understand the operational issues, we then went back to the drawing board to consider and determine the optimum system design.
Expert Investigation, Assessment & Analysis
An initial investigation and assessment of the site fish processing system and demands identified many key design issues including the vacuum headers, gut removal separators and carryover contamination of system components. These issues were adversely affecting/impacting the four automatic processing lines plus a hand finishing system for rejected fish.
The major issue with the previous salmon processing system was the misinterpretation and the incorrect application of pneumatic conveying principles – velocity transfers product (in this case fish waste) not vacuum. The original system had no velocity as the pipe was too big and each entry point was taken into the bottom of the pipe. This design was also resulting in a further issue as when automated system valves opened, waste was dropping and causing blockages through the system due to the oversized pipe.
Based on the incorrect assumption that larger units were required to transfer the waste, operating the problematical system were 3 off 30kW exhauster units connected to a large diameter ring main with an additional 45kW unit for the hand finishing line. This was resulting in high energy consumption and running costs for a system that was also needing 3-4 manual operatives due to a high fish rejection rate.
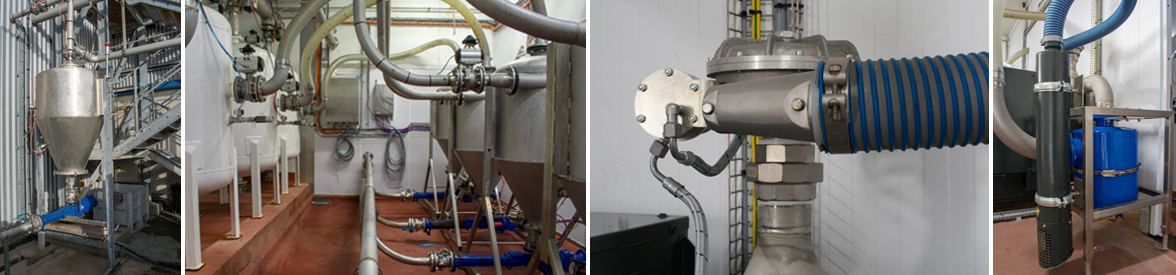
Pictured above (L to R) - External Cyclone Separator & Vacuum Line | Internal Separator Vessels & Cyclone Separators | Automatic Vacuum Control Valve | Vacuum Valve Silencer & Specialist SOLBERG Final Filter
Re-imagining & Designing the Optimum Vacuum System
As part of a comprehensive technical analysis and through discussions with our customer, we looked to establish key operating facts and parameters. This included:
- verification of the optimum processing rate per machine/line, establishing the number and size/weight of fish per hour
- an estimation of the rate of gut removal per machine based on the fish weight
- consideration of what flow was required at each nozzle, determined by the physical size of the gut removal nozzle and the removal line length per machine
Another consideration when re-designing the system focussed on each vertical take-off point where an air-operated valve opens and closes automatically for 0.5 seconds. There are four processing machines for the four lines, each installed with four sets of pipework. Being incorrectly sized with 4” piping this all had to be removed and replaced which was challenging as it was installed above the machines to each of the valves.
Going back to the drawing board and re-imagining the optimum system, our good friend and colleague, Derek Mayall, calculated and designed a completely new system to operate at a -350Mb (Millibar) vacuum. Based on an accurate processing rate and system length, he re-sized the vacuum headers to ensure that a constant conveying velocity is maintained throughout the process.
Effectively, there are four quality stages to the improved process:
- Q4 – with the fish already slit open, a vacuum nozzle is inserted into the fish to remove the majority of the gut
- Q2/Q3 – a finer nozzle is inserted deeper and along the backbone of the fish to remove further innards
- Q1 – is a final spray clean and rinse with filtered water
In addition, collection levels were considered in the cyclone separators to prevent carryover or contamination due to the vortex action, a specially designed interceptor vessel and wet-type line filters were introduced before the KAESER exhauster inlets along with vacuum control valves to prevent system ‘dead-heading’.
Innovative System Design & Advanced Technology
Interestingly, the only item from the original system reused was the cyclone. Having installed and commissioned the latest KAESER exhausters with advanced system technology, rigorous system tests and the initial process runs proved that the theoretical vacuum and extraction velocities were accurate and correct.
Following the installation of this innovative and bespoke new fish processing system, the previous system cleaning failure rate of circa 10% was reduced to less than 1%. This reduced the manpower required for hand cleaning drastically. Where there were previously 3-4 operatives manually cleaning the fish, now there is just one operative managing and attending all four process lines. This, in turn, has led to the redesign of the hand-finishing line.
Originally sized to take the full power from the previous 45 kW package, it has been possible to re-design and size the system with an 18.5 kW unit. Running variable speed for a much smaller header with two hand-cleaning tool lines running to a separator system, the unit operates at minimum frequency /speed for the hand-cleaning lines and maximum speed for the bulk removal of gut waste from the table collection hopper.
The new separator vessels were very effective and the in-line filter elements remained unchanged after 6 months of operation.
Cameron Kerr, Director, Kerr Compressor Engineers commented: "The bespoke vacuum system solution for the automated salmon processing lines was just one part of a larger multi-installation project across this impressive aquaculture site that we delivered for our customer." He continued; "Specialising in air solutions for both onshore and offshore applications, we specified and assisted with the installation of diesel-driven skid-mounted portable compressors on sea-pen support barges. In addition, we scoped, designed and installed a large onshore compressed air system that provides for all of the varied onsite air demands."
Speaking on behalf of everyone involved with this challenging project, Cameron added; "It was a great team effort and a pleasure to work in partnership with our friends and colleagues from our market-leading supplier partners." He finished by saying; "Following the success of this interesting project and having realised the significant cost savings and proven benefits from their investment in this bespoke system, our customer has confirmed orders with us to install similar systems for a further two processing lines."
A range of reliable, energy efficient KAESER air products including rotary screw compressors, diesel-driven skid-mounted portable compressors, low-pressure blower and vacuum systems plus high-quality air treatment products are specifically designed and built to provide maximum durability in Aquaculture environments and ensure maximum process reliability to minimise the risk of downtime.

Specialist KAESER Aquaculture Products & Solutions from Kerr Compressor Engineers
Compressed air, nitrogen and fluid power specialists in Scotland for over 40 years, Kerr is the UK's no.1 Authorised Distributor of KAESER KOMPRESSOREN / HPC compressed air systems and an experienced supplier to the Scottish Aquaculture community.
Operators of fish farms and Aquaculture sites throughout Scotland depend on reliable, quality supplies of low-pressure air, compressed air and vacuum. Our specialist aquaculture air solutions operate a variety of vital equipment, systems and processes for both onshore and offshore applications. Our products' impressive energy efficiency helps keep the largest part of total system costs to a minimum.
For further information and advice on specialised Aquaculture products and solutions, please contact our expert team on 0800 008 6588 - web.enquiry@kerrcompressors.co.uk
Read more on our Aquaculture Applications & Solutions page
Read our blog - 'Utilising Low Pressure Air & Compressed Air in Aquaculture'
Case Study Contributors/Credit:
Derek Mayall, KAESER HPC Applications Manager - Blowers
Adrian Feiler, KAESER Business Development Manager – Aquaculture
Recent Comments